Melting Technology
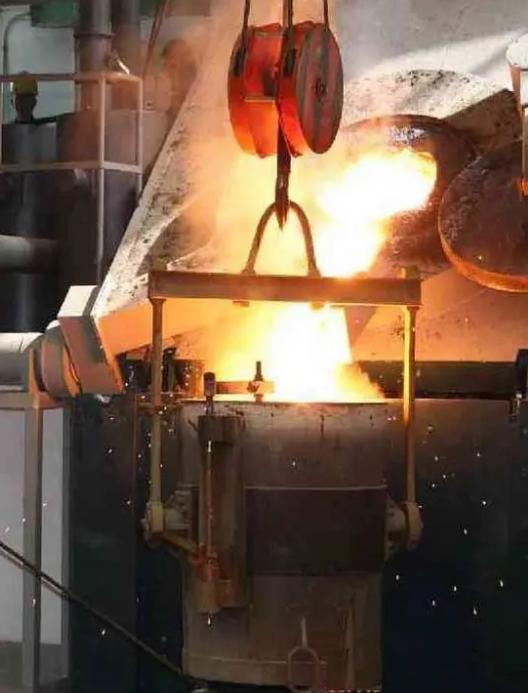
At present, the smelting of copper processing products generally adopts induction smelting furnace, and also adopts reverberatory furnace smelting and shaft furnace smelting.
Induction furnace smelting is suitable for all kinds of copper and copper alloys, and has the characteristics of clean smelting and ensuring the quality of the melt. According to the furnace structure, induction furnaces are divided into core induction furnaces and coreless induction furnaces. The cored induction furnace has the characteristics of high production efficiency and high thermal efficiency, and is suitable for continuous melting of a single variety of copper and copper alloys, such as red copper and brass. The coreless induction furnace has the characteristics of fast heating speed and easy replacement of alloy varieties. It is suitable for melting copper and copper alloys with high melting point and various varieties, such as bronze and cupronickel.
Vacuum induction furnace is an induction furnace equipped with a vacuum system, suitable for smelting copper and copper alloys that are easy to inhale and oxidize, such as oxygen-free copper, beryllium bronze, zirconium bronze, magnesium bronze, etc. for electric vacuum.
Reverberatory furnace smelting can refine and remove impurities from the melt, and is mainly used in the smelting of scrap copper. The shaft furnace is a kind of rapid continuous melting furnace, which has the advantages of high thermal efficiency, high melting rate, and convenient furnace shutdown. Can be controlled; there is no refining process, so the vast majority of raw materials are required to be cathode copper. Shaft furnaces are generally used with continuous casting machines for continuous casting, and can also be used with holding furnaces for semi-continuous casting.
The development trend of copper smelting production technology is mainly reflected in reducing the burning loss of raw materials, reducing the oxidation and inhalation of the melt, improving the quality of the melt, and adopting high efficiency (the melting rate of the induction furnace is greater than 10 t/h), large-scale (the capacity of the induction furnace can be greater than 35 t/set), long life (the lining life is 1 to 2 years) and energy-saving (the energy consumption of the induction furnace is less than 360 kW h/t), the holding furnace is equipped with a degassing device (CO gas degassing), and the induction furnace The sensor adopts spray structure, the electric control equipment adopts bidirectional thyristor plus frequency conversion power supply, the furnace preheating, the furnace condition and refractory temperature field monitoring and alarm system, the holding furnace is equipped with a weighing device, and the temperature control is more accurate.
Production Equipment - Slitting Line
The production of copper strip slitting line is a continuous slitting and slitting production line that widens the wide coil through the uncoiler, cuts the coil into the required width through the slitting machine, and rewinds it into several coils through the winder.(Storage Rack) Use a crane to store the rolls on the storage rack
↓
(Loading car) Use the feeding trolley to manually put the material roll on the uncoiler drum and tighten it up
↓
(Uncoiler and anti-loosening pressure roller) Unwind the coil with the help of the opening guide and pressure roller
↓
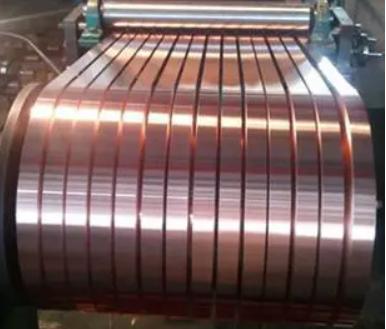
(NO·1 looper and swing bridge) storage and buffer
↓
(Edge guide and pinch roller device) Vertical rollers guide the sheet into the pinch rollers to prevent deviation, vertical guide roller width and positioning are adjustable
↓
(Slitting machine) enter the slitting machine for positioning and slitting
↓
(Quick-change rotary seat) Tool group exchange
↓
(Scrap winding device) Cut the scrap
↓(Outlet end guide table and coil tail stopper) Introduce NO.2 looper
↓
(swing bridge and NO.2 looper) material storage and elimination of thickness difference
↓
(Press plate tension and air expansion shaft separation device) provide tension force, plate and belt separation
↓
(Slitting shear, steering length measuring device and guide table) length measuring, coil fixed-length segmentation, tape threading guide
↓
(winder, separation device, push plate device) separator strip, coiling
↓
(unloading truck, packaging) copper tape unloading and packaging
Hot Rolling Technology
Hot rolling is mainly used for billet rolling of ingots for sheet, strip and foil production.
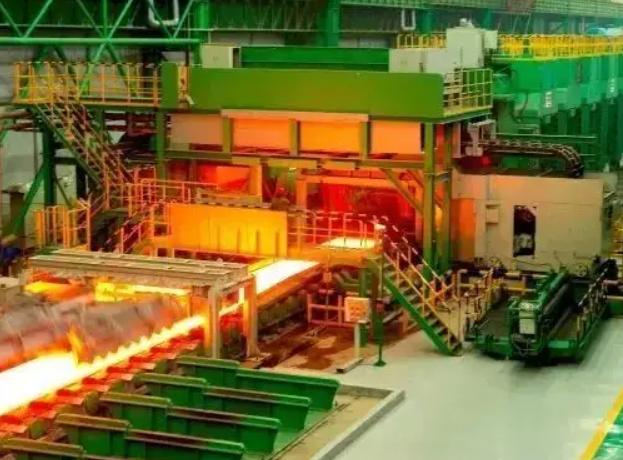
Ingot specifications for billet rolling should consider factors such as product variety, production scale, casting method, etc., and are related to rolling equipment conditions (such as roll opening, roll diameter, allowable rolling pressure, motor power, and roller table length), etc. . Generally, the ratio between the thickness of the ingot and the diameter of the roll is 1: (3.5~7): the width is usually equal to or several times the width of the finished product, and the width and trimming amount should be properly considered. Generally, the width of the slab should be 80% of the length of the roll body. The length of the ingot should be reasonably considered according to the production conditions. Generally speaking, under the premise that the final rolling temperature of hot rolling can be controlled, the longer the ingot, the higher the production efficiency and yield.
The ingot specifications of small and medium-sized copper processing plants are generally (60 ~ 150) mm × (220 ~ 450) mm × (2000 ~ 3200) mm, and the ingot weight is 1.5 ~ 3 t; the ingot specifications of large copper processing plants Generally, it is (150~250)mm×(630~1250)mm×(2400~8000)mm, and the weight of the ingot is 4.5~20 t.
During hot rolling, the temperature of the roll surface rises sharply at the moment when the roll is in contact with the high-temperature rolling piece. Repeated thermal expansion and cold contraction cause cracks and cracks on the surface of the roll. Therefore, cooling and lubrication must be performed during hot rolling. Usually, water or a lower concentration emulsion is used as the cooling and lubricating medium. The total working rate of hot rolling is generally 90% to 95%. The thickness of the hot-rolled strip is generally 9 to 16 mm. Surface milling of strip after hot rolling can remove surface oxide layers, scale intrusions and other surface defects produced during casting, heating and hot rolling. According to the severity of the surface defects of the hot-rolled strip and the needs of the process, the milling amount of each side is 0.25 to 0.5 mm.
Hot rolling mills are generally two-high or four-high reversing rolling mills. With the enlargement of the ingot and the continuous lengthening of the strip length, the control level and function of the hot rolling mill have a trend of continuous improvement and improvement, such as the use of automatic thickness control, hydraulic bending rolls, front and rear vertical rolls, only cooling rolls without cooling Rolling device device, TP roll (Taper Pis-ton Roll) crown control, online quenching (quenching) after rolling, online coiling and other technologies to improve the uniformity of the strip structure and properties and obtain better plate.
Casting Technology
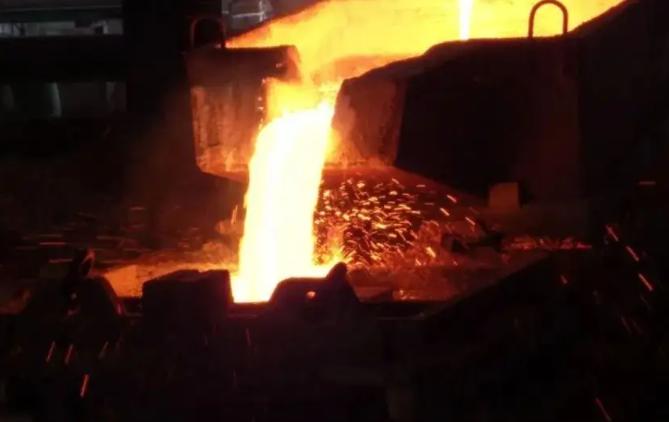
The casting of copper and copper alloys is generally divided into: vertical semi-continuous casting, vertical full continuous casting, horizontal continuous casting, upward continuous casting and other casting technologies.
A. Vertical Semi-continuous Casting
Vertical semi-continuous casting has the characteristics of simple equipment and flexible production, and is suitable for casting various round and flat ingots of copper and copper alloys. The transmission mode of vertical semi-continuous casting machine is divided into hydraulic, lead screw and wire rope. Because the hydraulic transmission is relatively stable, it has been more used. The crystallizer can be vibrated with different amplitudes and frequencies as required. At present, the semi-continuous casting method is widely used in the production of copper and copper alloy ingots.
B. Vertical full Continuous Casting
Vertical full continuous casting has the characteristics of large output and high yield (about 98%), suitable for large-scale and continuous production of ingots with a single variety and specification, and is becoming one of the main selection methods for the melting and casting process on modern large-scale copper strip production lines . The vertical full continuous casting mold adopts non-contact laser liquid level automatic control. The casting machine generally adopts hydraulic clamping, mechanical transmission, online oil-cooled dry chip sawing and chip collection, automatic marking, and tilting the ingot. The structure is complex and the degree of automation is high.
C. Horizontal Continuous Casting
Horizontal continuous casting can produce billets and wire billets.
Strip horizontal continuous casting can produce copper and copper alloy strips with a thickness of 14-20mm. Strips in this thickness range can be directly cold-rolled without hot rolling, so they are often used to produce alloys that are difficult to hot-roll (such as tin. Phosphor bronze, lead brass, etc.), can also produce brass, cupronickel and low alloyed copper alloy strip. Depending on the width of the casting strip, horizontal continuous casting can cast 1 to 4 strips at the same time. Commonly used horizontal continuous casting machines can cast two strips at the same time, each with a width of less than 450 mm, or cast one strip with a strip width of 650-900 mm. The horizontal continuous casting strip generally adopts the casting process of pull-stop-reverse push, and there are periodic crystallization lines on the surface, which should generally be eliminated by milling. There are domestic examples of high-surface copper strips that can be produced by drawing and casting strip billets without milling.
Horizontal continuous casting of tube, rod and wire billets can cast 1 to 20 ingots at the same time according to different alloys and specifications. Generally, the diameter of the bar or wire blank is 6 to 400 mm, and the outer diameter of the tube blank is 25 to 300 mm. The wall thickness is 5-50 mm, and the side length of the ingot is 20-300 mm. The advantages of the horizontal continuous casting method are that the process is short, the manufacturing cost is low, and the production efficiency is high. At the same time, it is also a necessary production method for some alloy materials with poor hot workability. Recently, it is the main method for making billets of commonly used copper products such as tin-phosphor bronze strips, zinc-nickel alloy strips, and phosphorus-deoxidized copper air-conditioning pipes. production methods.
The disadvantages of the horizontal continuous casting production method are: the suitable alloy varieties are relatively simple, the consumption of the graphite material in the mold inner sleeve is relatively large, and the uniformity of the crystalline structure of the cross section of the ingot is not easy to control. The lower part of the ingot is continuously cooled due to the effect of gravity, which is close to the inner wall of the mold, and the grains are finer; the upper part is due to the formation of air gaps and the high melt temperature, which causes the lag in solidification of the ingot, which slows down the cooling rate and makes the ingot solidification hysteresis. The crystalline structure is relatively coarse, which is especially obvious for large-sized ingots. In view of the above shortcomings, the vertical bending casting method with billet is currently being developed. A German company used a vertical bending continuous caster to test-cast (16-18) mm × 680 mm tin bronze strips such as DHP and CuSn6 at a speed of 600 mm/min.
D. Upward Continuous Casting
Upward continuous casting is a casting technology that has developed rapidly in the past 20 to 30 years, and is widely used in the production of wire billets for bright copper wire rods. It utilizes the principle of vacuum suction casting and adopts stop-pull technology to realize continuous multi-head casting. It has the characteristics of simple equipment, small investment, less metal loss, and low environmental pollution procedures. Upward continuous casting is generally suitable for the production of red copper and oxygen-free copper wire billets. The new achievement developed in recent years is its popularization and application in large-diameter tube blanks, brass and cupronickel. At present, an upward continuous casting unit with an annual output of 5,000 t and a diameter of more than Φ100 mm has been developed; binary ordinary brass and zinc-white copper ternary alloy wire billets have been produced, and the yield of the wire billets can reach more than 90%.
E. Other Casting Techniques
The continuous casting billet technology is under development. It overcomes the defects such as slub marks formed on the outer surface of the billet due to the stop-pull process of the upward continuous casting, and the surface quality is excellent. And because of its nearly directional solidification characteristics, the internal structure is more uniform and pure, so the performance of the product is also better. The production technology of belt type continuous casting copper wire billet has been widely used in large production lines above 3 tons. The cross-sectional area of the slab is generally more than 2000 mm2, and it is followed by a continuous rolling mill with high production efficiency.
Electromagnetic casting has been tried in my country as early as the 1970s, but industrial production has not been realized. In recent years, electromagnetic casting technology has made great progress. At present, oxygen-free copper ingots of Φ200 mm have been successfully cast with smooth surface. At the same time, the stirring effect of the electromagnetic field on the melt can promote exhaust and slag removal, and oxygen-free copper with an oxygen content of less than 0.001% can be obtained.
The direction of the new copper alloy casting technology is to improve the structure of the mold through directional solidification, rapid solidification, semi-solid forming, electromagnetic stirring, metamorphic treatment, automatic control of liquid level and other technical means according to the solidification theory. , densification, purification, and realize continuous operation and near-end forming.
In the long run, the casting of copper and copper alloys will be the coexistence of semi-continuous casting technology and full continuous casting technology, and the application proportion of continuous casting technology will continue to increase.
Cold Rolling Technology
According to the rolled strip specification and rolling process, cold rolling is subdivided into blooming, intermediate rolling and finishing rolling. The process of cold rolling the cast strip with a thickness of 14 to 16 mm and the hot rolled billet with a thickness of about 5 to 16 mm to 2 to 6 mm is called blooming, and the process of continuing to reduce the thickness of the rolled piece is called intermediate rolling. , the final cold rolling to meet the requirements of the finished product is called finish rolling.
The cold rolling process needs to control the reduction system (total processing rate, pass processing rate and finished product processing rate) according to different alloys, rolling specifications and finished product performance requirements, reasonably select and adjust the roll shape, and reasonably select the lubrication method and lubricant. Tension measurement and adjustment.
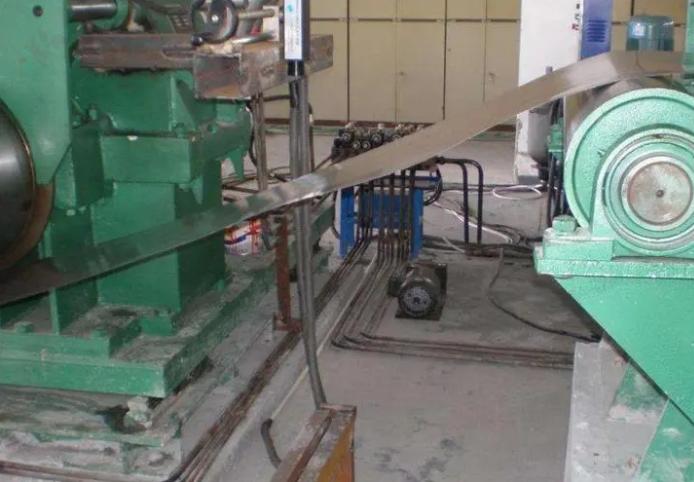
Cold rolling mills generally use four-high or multi-high reversing rolling mills. Modern cold rolling mills generally use a series of technologies such as hydraulic positive and negative roll bending, automatic control of thickness, pressure and tension, axial movement of rolls, segmental cooling of rolls, automatic control of plate shape, and automatic alignment of rolled pieces, so that the accuracy of the strip can be improved. Up to 0.25±0.005 mm and within 5I of plate shape.
The development trend of cold rolling technology is reflected in the development and application of high-precision multi-roll mills, higher rolling speeds, more accurate strip thickness and shape control, and auxiliary technologies such as cooling, lubrication, coiling, centering and rapid roll change. refinement, etc.
Production Equipment-Bell Furnace
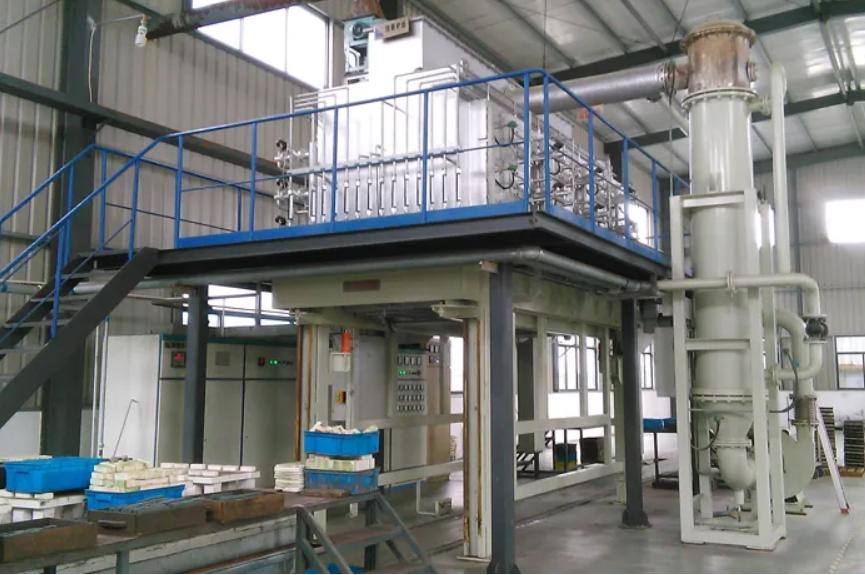
Bell jar furnaces and lifting furnaces are generally used in industrial production and pilot tests. Generally, the power is large and the power consumption is large. For industrial enterprises, the furnace material of Luoyang Sigma lifting furnace is ceramic fiber, which has good energy saving effect, low energy consumption, and low energy consumption. Save electricity and time, which is beneficial to increase production.
Twenty-five years ago, Germany's BRANDS and Philips, a leading company in the ferrite manufacturing industry, jointly developed a new sintering machine. The development of this equipment caters to the special needs of the ferrite industry. During this process, the BRANDS Bell Furnace is continuously updated.
He pays attention to the needs of world-renowned companies such as Philips, Siemens, TDK, FDK, etc., which also benefit greatly from the high-quality equipment of BRANDS.
Due to the high stability of the products produced by bell furnaces, bell furnaces have become the top companies in the professional ferrite production industry. Twenty-five years ago, the first kiln made by BRANDS is still producing high-quality products for Philips.
The main characteristic of the sintering furnace offered by the bell furnace is its high efficiency. Its intelligent control system and other equipment form a complete functional unit, which can fully meet the almost state-of-the-art requirements of the ferrite industry.
Bell jar furnace customers can program and store any temperature/atmosphere profile required to produce high quality products. In addition, customers can also produce any other products in time according to actual needs, thereby shortening lead times and reducing costs. The sintering equipment must have good adjustability to produce a variety of different products to continuously adapt to the needs of the market. This means that the corresponding products must be produced according to the needs of the individual customer.
A good ferrite manufacturer can produce more than 1000 different magnets to meet the special needs of customers. These require the ability to repeat the sintering process with high precision. Bell jar furnace systems have become standard furnaces for all ferrite producers.
In the ferrite industry, these furnaces are mainly used for low power consumption and high μ value ferrite, especially in the communication industry. It is impossible to produce high quality cores without a bell furnace.
The bell furnace requires only a few operators during sintering, loading and unloading can be completed during the day, and sintering can be completed at night, enabling peak shaving of electricity, which is very practical in today's power shortage situation. Bell jar furnaces produce high-quality products, and all additional investments are quickly recouped due to high-quality products. Temperature and atmosphere control, furnace design and airflow control within the furnace are all perfectly integrated to ensure uniform product heating and cooling. The control of the kiln atmosphere during cooling is directly related to the kiln temperature and can guarantee an oxygen content of 0.005% or even lower. And these are things our competitors can't do.
Thanks to the complete alphanumeric programming input system, long sintering processes can be easily replicated, thus ensuring product quality. When selling a product, it is also a reflection of the quality of the product.
Heat Treatment Technology
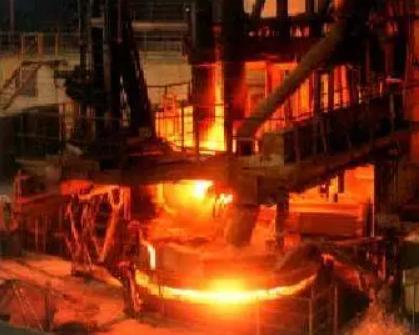
A few alloy ingots (strips) with severe dendrite segregation or casting stress, such as tin-phosphor bronze, need to undergo special homogenization annealing, which is generally carried out in a bell jar furnace. The homogenization annealing temperature is generally between 600 and 750°C.
At present, most of the intermediate annealing (recrystallization annealing) and finished annealing (annealing to control the state and performance of the product) of copper alloy strips are bright annealed by gas protection. The furnace types include bell jar furnace, air cushion furnace, vertical traction furnace, etc. Oxidative annealing is being phased out.
The development trend of heat treatment technology is reflected in the hot rolling on-line solution treatment of precipitation-strengthened alloy materials and the subsequent deformation heat treatment technology, continuous bright annealing and tension annealing in a protective atmosphere.
Quenching—Aging heat treatment is mainly used for heat-treatable strengthening of copper alloys. Through heat treatment, the product changes its microstructure and obtains the required special properties. With the development of high-strength and high-conductivity alloys, the quenching-aging heat treatment process will be more applied. The aging treatment equipment is roughly the same as the annealing equipment.
Extrusion Technology
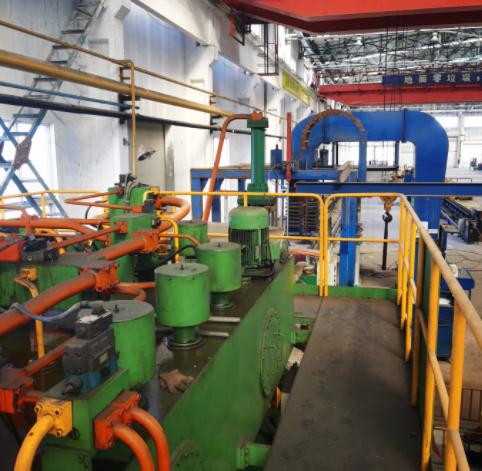
Extrusion is a mature and advanced copper and copper alloy pipe, rod, profile production and billet supply method. By changing the die or using the method of perforation extrusion, various alloy varieties and different cross-sectional shapes can be directly extruded. Through extrusion, the cast structure of the ingot is changed into a processed structure, and the extruded tube billet and bar billet have high dimensional accuracy, and the structure is fine and uniform. The extrusion method is a production method commonly used by domestic and foreign copper pipe and rod manufacturers.
Copper alloy forging is mainly carried out by machinery manufacturers in my country, mainly including free forging and die forging, such as large gears, worm gears, worms, automobile synchronizer gear rings, etc.
The extrusion method can be divided into three types: forward extrusion, reverse extrusion and special extrusion. Among them, there are many applications of forward extrusion, reverse extrusion is used in the production of small and medium-sized rods and wires, and special extrusion is used in special production.
When extruding, according to the properties of the alloy, the technical requirements of the extruded products, and the capacity and structure of the extruder, the type, size and extrusion coefficient of the ingot should be reasonably selected, so that the degree of deformation is not less than 85%. The extrusion temperature and extrusion speed are the basic parameters of the extrusion process, and the reasonable extrusion temperature range should be determined according to the plasticity diagram and phase diagram of the metal. For copper and copper alloys, the extrusion temperature is generally between 570 and 950 °C, and the extrusion temperature from copper is even as high as 1000 to 1050 °C. Compared with the extrusion cylinder heating temperature of 400 to 450 °C, the temperature difference between the two is relatively high. If the extrusion speed is too slow, the temperature of the surface of the ingot will drop too fast, resulting in an increase in the unevenness of the metal flow, which will lead to an increase in the extrusion load, and even cause a boring phenomenon. Therefore, copper and copper alloys generally use relatively High-speed extrusion, the extrusion speed can reach more than 50 mm/s.
When copper and copper alloys are extruded, peeling extrusion is often used to remove surface defects of the ingot, and the peeling thickness is 1-2 m. Water sealing is generally used at the exit of the extrusion billet, so that the product can be cooled in the water tank after extrusion, and the surface of the product is not oxidized, and subsequent cold processing can be carried out without pickling. It tends to use a large-tonnage extruder with a synchronous take-up device to extrude tube or wire coils with a single weight of more than 500 kg, so as to effectively improve the production efficiency and comprehensive yield of the subsequent sequence. At present, the production of copper and copper alloy pipes mostly adopts horizontal hydraulic forward extruders with independent perforation system (double-action) and direct oil pump transmission, and the production of bars mostly adopts non-independent perforation system (single-action) and oil pump direct transmission. Horizontal hydraulic forward or reverse extruder. The commonly used extruder specifications are 8-50 MN, and now it tends to be produced by large-tonnage extruders above 40 MN to increase the single weight of the ingot, thereby improving production efficiency and yield.
Modern horizontal hydraulic extruders are structurally equipped with prestressed integral frame, extrusion barrel "X" guide and support, built-in perforation system, perforation needle internal cooling, sliding or rotary die set and rapid Die changing device, high-power variable oil pump direct drive, integrated logic valve, PLC control and other advanced technologies, the equipment has high precision, compact structure, stable operation, safe interlocking, and easy to realize program control. Continuous extrusion (Conform) technology has made some progress in the past ten years, especially for the production of special-shaped bars such as electric locomotive wires, which is very promising. In recent decades, new extrusion technology has developed rapidly, and the development trend of extrusion technology is embodied as follows: (1) Extrusion equipment. The extrusion force of the extrusion press will develop in a greater direction, and the extrusion press of more than 30MN will become the main body, and the automation of the extrusion press production line will continue to improve. Modern extrusion machines have completely adopted computer program control and programmable logic control, so that production efficiency is greatly improved, operators are significantly reduced, and it is even possible to realize automatic unmanned operation of extrusion production lines.
The body structure of the extruder has also been continuously improved and perfected. In recent years, some horizontal extruders have adopted a prestressed frame to ensure the stability of the overall structure. The modern extruder realizes the forward and reverse extrusion methods. The extruder is equipped with two extrusion shafts (main extrusion shaft and die shaft). During extrusion, the extrusion cylinder moves with the main shaft. At this time, the product is The outflow direction is consistent with the moving direction of the main shaft and opposite to the relative moving direction of the die axis. The die base of the extruder also adopts the configuration of multiple stations, which not only facilitates die change, but also improves the production efficiency. Modern extruders use a laser deviation adjustment control device, which provides effective data on the state of the extrusion center line, which is convenient for timely and rapid adjustment. The high-pressure pump direct-drive hydraulic press using oil as the working medium has completely replaced the hydraulic press. Extrusion tools are also constantly updated with the development of extrusion technology. The internal water cooling piercing needle has been widely promoted, and the variable cross-section piercing and rolling needle greatly improves the lubrication effect. Ceramic molds and alloy steel molds with longer life and higher surface quality are more widely used.
Extrusion tools are also constantly updated with the development of extrusion technology. The internal water cooling piercing needle has been widely promoted, and the variable cross-section piercing and rolling needle greatly improves the lubrication effect. The application of ceramic molds and alloy steel molds with longer life and higher surface quality is more popular. (2) Extrusion production process. The varieties and specifications of extruded products are constantly expanding. The extrusion of small-section, ultra-high-precision tubes, rods, profiles and super-large profiles ensures the appearance quality of products, reduces internal defects of products, reduces geometric loss, and further promotes extrusion methods such as uniform performance of extruded products. Modern reverse extrusion technology is also widely used. For easily oxidized metals, water seal extrusion is adopted, which can reduce pickling pollution, reduce metal loss, and improve the surface quality of products. For extruded products that need to be quenched, just control the appropriate temperature. The water seal extrusion method can achieve the purpose, effectively shorten the production cycle and save energy.
With the continuous improvement of extruder capacity and extrusion technology, modern extrusion technology has been gradually applied, such as isothermal extrusion, cooling die extrusion, high-speed extrusion and other forward extrusion technologies, reverse extrusion, hydrostatic extrusion The practical application of continuous extrusion technology of pressing and Conform, the application of powder extrusion and layered composite extrusion technology of low temperature superconducting materials, the development of new methods such as semi-solid metal extrusion and multi-blank extrusion, the development of small precision parts Cold extrusion forming technology, etc., have been rapidly developed and widely developed and applied.
Spectrometer
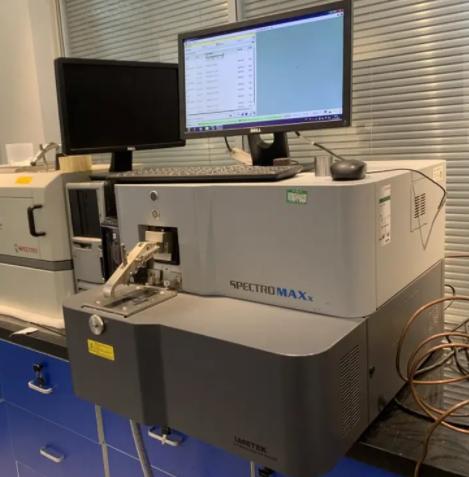
Spectroscope is a scientific instrument that decomposes light with complex composition into spectral lines. The seven-color light in sunlight is the part that the naked eye can distinguish (visible light), but if sunlight is decomposed by a spectrometer and arranged according to wavelength, visible light only occupies a small range in the spectrum, and the rest are spectrums that cannot be distinguished by the naked eye, such as infrared rays, microwaves , UV rays, X-rays, etc. The optical information is captured by the spectrometer, developed with a photographic film, or displayed and analyzed by a computerized automatic display numerical instrument, so as to detect what elements are contained in the article. This technology is widely used in the detection of air pollution, water pollution, food hygiene, metal industry, etc.
Spectrometer, also known as spectrometer, is widely known as direct reading spectrometer. A device that measures the intensity of spectral lines at different wavelengths with photodetectors such as photomultiplier tubes. It consists of an entrance slit, a dispersive system, an imaging system and one or more exit slits. The electromagnetic radiation of the radiation source is separated into the required wavelength or wavelength region by the dispersive element, and the intensity is measured at the selected wavelength (or scanning a certain band). There are two types of monochromators and polychromators.
Testing Instrument-Conductivity Meter
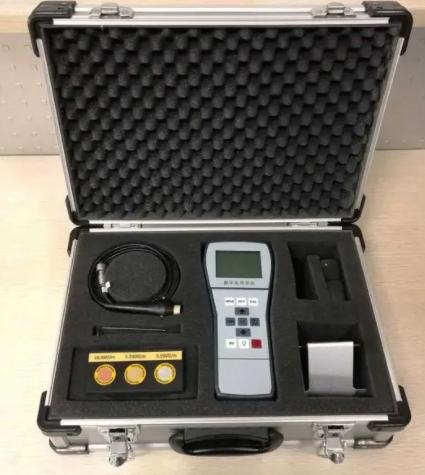
The digital hand-held metal conductivity tester (conductivity meter) FD-101 applies the principle of eddy current detection and is specially designed according to the conductivity requirements of the electrical industry. It meets the testing standards of the metal industry in terms of function and accuracy.
1. Eddy current conductivity meter FD-101 has three unique:
1) The only Chinese conductivity meter that has passed the verification of the Institute of Aeronautical Materials;
2) The only Chinese conductivity meter that can meet the needs of aircraft industry companies;
3) The only Chinese conductivity meter exported to many countries.
2. Product function introduction:
1) Large measuring range: 6.9%IACS-110%IACS(4.0MS/m-64MS/m), which meets the conductivity test of all non-ferrous metals.
2) Intelligent calibration: fast and accurate, completely avoiding manual calibration errors.
3) The instrument has good temperature compensation: the reading is automatically compensated to the value at 20 °C, and the correction is not affected by human error.
4) Good stability: it is your personal guard for quality control.
5) Humanized intelligent software: It brings you a comfortable detection interface and powerful data processing and collection functions.
6) Convenient operation: the production site and laboratory can be used everywhere, winning the favor of the majority of users.
7) Self-replacement of probes: Each host can be equipped with multiple probes, and users can replace them at any time.
8) Numerical resolution: 0.1%IACS (MS/m)
9) The measurement interface simultaneously displays the measurement values in two units of %IACS and MS/m.
10) It has the function of holding measurement data.
Hardness Tester
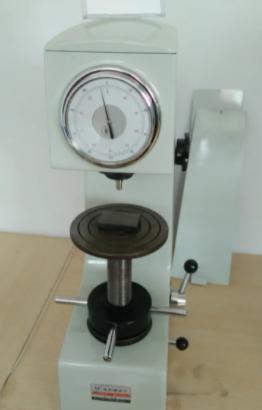
The instrument adopts a unique and precise design in mechanics, optics and light source, which makes the indentation imaging clearer and the measurement more accurate. Both 20x and 40x objective lenses can participate in the measurement, making the measurement range larger and the application more extensive. The instrument is equipped with a digital measuring microscope, which can display the test method, test force, indentation length, hardness value, test force holding time, measurement times, etc. on the liquid screen, and has a threaded interface that can be connected to a digital camera and a CCD camera. It has a certain representativeness in domestic head products.
Testing Instrument-Resistivity Detector
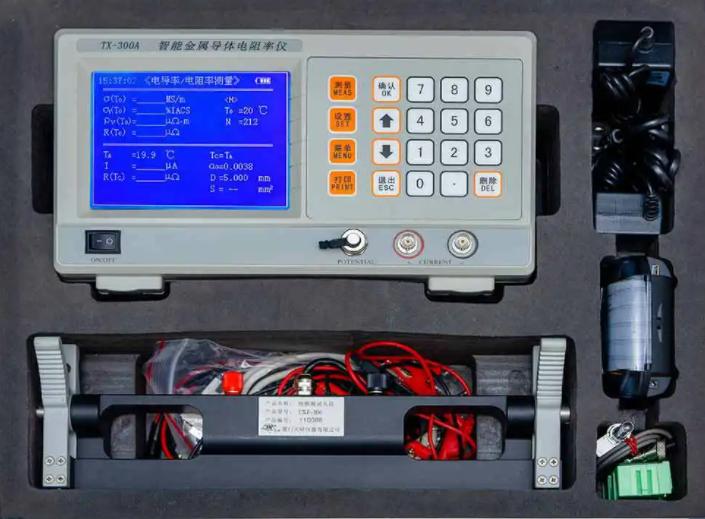
The metal wire resistivity measuring instrument is a high-performance testing instrument for parameters such as wire, bar resistivity and electrical conductivity. Its performance fully complies with the relevant technical requirements in GB/T3048.2 and GB/T3048.4. Widely used in metallurgy, electric power, wire and cable, electrical appliances, colleges and universities, scientific research units and other industries.
Main features of the instrument:
(1) It integrates advanced electronic technology, single-chip technology and automatic detection technology, with strong automation function and simple operation;
(2) Just press the key once, all measured values can be obtained without any calculation, suitable for continuous, fast and accurate detection;
(3) Battery-powered design, small size, easy to carry, suitable for field and field use;
(4) Large screen, large font, can display resistivity, conductivity, resistance and other measured values and temperature, test current, temperature compensation coefficient and other auxiliary parameters at the same time, very intuitive;
(5) One machine is multi-purpose, with 3 measurement interfaces, namely conductor resistivity and conductivity measurement interface, cable comprehensive parameter measurement interface, and cable DC resistance measurement interface (TX-300B type);
(6) Each measurement has the functions of automatic selection of constant current, automatic current commutation, automatic zero point correction, and automatic temperature compensation correction to ensure the accuracy of each measurement value;
(7) The unique portable four-terminal test fixture is suitable for rapid measurement of different materials and different specifications of wires or bars;
(8) Built-in data memory, which can record and save 1000 sets of measurement data and measurement parameters, and connect to the upper computer to generate a complete report.